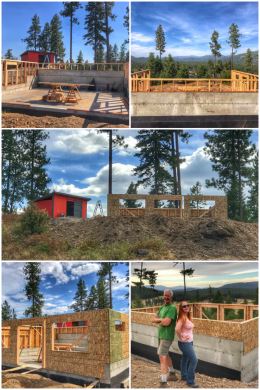
We’re building on raw land in Eastern Washington… in 2020… fighting the bizarre results from the COVID pandemic, including shortages of both labor and supplies, price-gouging by some contractors, and delays in getting inspections… but the good news is that the building is moving forward, albeit a bit slower and costlier than we expected.
We last left off with all the concrete work completed… and it was such a joy when the basement walls were finally framed and we could see and smell the wonderful wood shaping our carefully-designed little future home. The picture in the lower right corner is celebrating both the completion of the basement framing — and the anniversary of our first meeting (interestingly, also in Eastern Washginton).
The building process is so much hurry up and wait… hurry up to get supplies and circumstances ready and then wait for the inspection or for workers to show up. Don’t get us wrong, we are thrilled to death that the framing finally got started — it’s just we expected to be at this place about two months ago.
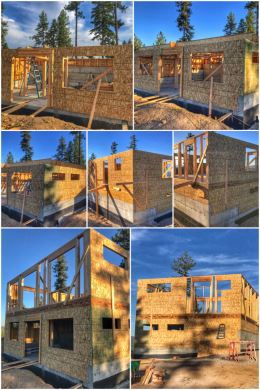
But then, almost in the blink of the eye, the first floor was being framed.
We were so excited to see the walls of the first floor rise on top of the basement – and to see all the windows we had planned to admire the views of the lake and mountains.
Speaking of windows, we purposely placed our order weeks ago in case there were any delays in manufacturing and delivering. All our windows and French Doors did arrive on time and were stashed away in the basement for safe-keeping (which you can see in the collage below). Our front door and the two “man” doors for the garage are missing in action — but we hope to have them by the middle of October.
We also took advantage of some Labor Day sales to purchase new furniture needed for the first floor (where we will live while we finish the basement and upper floor). We helped the economy by purchasing a dining table and chairs, a sectional for the living room, and a platform for our Sleep Number bed for the guest bedroom. Already on order are the kitchen cabinets and quartz countertops, as well as the main floor bathroom supplies (including cabinet, sink, toilet, bathtub, and plumbing fixtures.
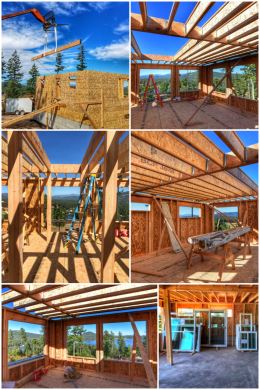
It was even more exciting seeing the second/top floor being framed!
We designed the top floor as one massive master space — with a bedroom, bathroom, walk-in closet, sitting room, and office.
While we purposely created two master bedrooms in the house for the day when one of us might not be physically able to climb all the stairs to the upper floor, we really hope that never happens as the top floor suite is going to be so amazing… so amazing that we joked that we will get one of those seat elevators for the stairs to keep us up there for as long as possible.
While the framers were doing their thing, we kept busy working on the property — including a lot of moving dirt to help backfill around most of the foundation walls. (We need to leave two corners open for the sewer, water, and electric to head down to our septic tank and future RV pad.
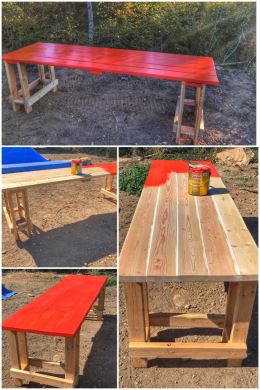
Ran also kept busy with another reclaimed wood furniture project — this time designing and building a workbench from the unusable 2×6 boards meant for the house. (It’s a long story, but we got a delivery of #3 pine boards for free, which was a good thing as many of the boards were damaged or warped.
Total cost was about $10 — for a tube of caulk to help fill the holes in the boards and for a box of deck screws. We already had the glue, sandpaper, and paint. Before it heads into the workshop, we will probably use it as a staging platform for when we have our “Construction is Finished” party, which we hope will be in late October.
That date keeps moving around — mostly because of COVID, but also because the smoke from the western wildfires made the air quality so bad for about a week that the crew took a few days off from working, further slowing our progress.
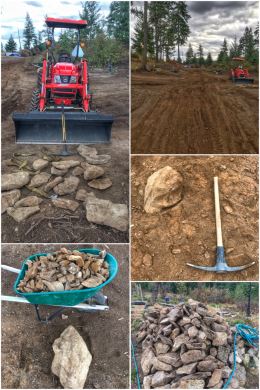
Finally, we try each day to do whatever we can to keep the build moving forward — whether that is picking up scrap pieces of wood or keeping the building site organized. We also spent a day using the tractor to smooth down the driveway between the house and the garage — unearthing quite a few rocks of all sizes and shapes in the process. And yes, we needed to use the pick axe for a few of the bigger rocks! (We plan to relocate the bigger rocks for a pond and retaining wall.)
Next up? We look for the roof trusses, Tyvek, and drying in the house… as well as one or two more reclaimed wood projects.